Batteries are complex electro-chemical devices and sensitive to operator mistakes and charging system configuration errors. Just a couple of deep discharge cycles can lead to early failure. Long periods without fully charging can reduce the capacity of a battery bank. Equalization (extended charge periods at controlled high-voltage charging) can partially reverse some of these effects, but the improvement from equalization is only partial. And, equalizing too frequently can also reduce battery operating lifetime.
To learn more about battery lifecycles, we capture battery voltage and charge/discharge amperage every five seconds in a database, and have been doing this for nearly nine years. This post looks at this data and draws some conclusions. The discussion focuses on lead-acid battery chemistries—our house bank consist of eight Lifeline 8D batteries. Li-Ion chemistries have some characteristics in common, but differ in important ways like being far more tolerant of deep discharge.
From our perspective, the most important factor is to ensure battery float, absorption and bulk charging parameters are both temperature-corrected and match the manufacturer specs. This isn’t hard to do and it’s an easy way to improve battery lifetime. Of course we do that and, in addition, we also have alarms and send email on any out-of-specification operating condition. This is a bit more work to set up, but the returns in increased battery life can pay for monitoring systems fairly quickly, so we do this as well.
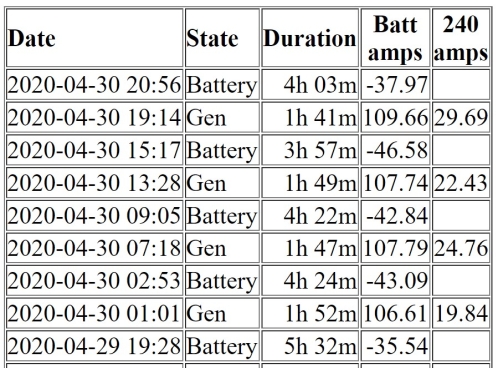
Since we record battery voltage and charge/discharge amperage every five seconds we are able to check to see if we have made any operating mistakes over the entire multi-year lifetime of a given battery bank. Our first set of batteries did see some operator errors where they were excessively discharged during their lifetime. To make the boat easier to operate, to ensure the batteries never deeply discharge, and to allow us to be away from the boat for more than a battery discharge cycle, we installed generator auto-start early in the boat’s lifetime.
Auto-start has been a real blessing, and it’s only because of this feature that our second set of batteries, went their entire lifetime without a single excessively deep discharge cycle. They have never been down below 50% charge. Avoiding deep discharge allowed us to reach over 1,500 cycles when Lifeline reports their batteries are good for 1,000 cycles at no more than 50% discharge. The only way we were able to get this high cycle count is through a combination of never excessively discharging them and continuing to use the batteries when the capacity had fallen to between a quarter and a third of their original design specification.
![]() |
![]() |
On our boat, operating a battery bank with such a reduced capacity requires running the generator at least every three hours. This would be an inconvenience were it a manual operation. But, when handled by automation, the generator just runs more frequently and it’s otherwise not noticeable. Having the ability to use the batteries far longer (effectively extending their usable lifetime), has two big advantages. The first is that a given battery bank investment can be used longer, reducing the effective cost of the battery bank. The second advantage is more subtle: when you are planning a trip and the batteries are in serviceable but not great condition, there is great temptation to just replace them to avoid getting let down when away from civilization. We are careful but, since we know we can use the batteries to end of life, we aren’t tempted to change them early. We just run the batteries until they are nearly out of capacity.
![]() |
![]() |
Battery capacity tends to slowly decrease over time. Except for rare faults where batteries have a mechanical failure such as warped plates, or suffer from thermal overload, the capacity just slowly diminishes over time. We don’t worry about these rare fault modes, since our boat has four parallel and independent groups of two batteries each. If a battery suffers a sudden, serious failure, a single flip of a switch takes that pair of batteries out of rotation and the boat continues to operate with three quarters of the designed battery bank capacity.
We have evolved to a model where we basically ignore the generator and rely nearly exclusively on auto-start. In fact, we have become so dependent upon auto-start that we installed it on a second generator (two generators when you only have one). Generator auto-start is very helpful in extracting the last bit of value out of a bank and we suspect that, without this feature, instead of getting 1,500 cycles from our last set of batteries, it would have been far less than 1,000 cycles.
Looking at the data below, we will track a new set batteries throughout their lifetime looking first at performance when new, the performance after a couple of years of full-time live aboard use, and finally we look at their performance at end-of-life. Then we check battery performance for the first two years of a new battery bank to see if the original results are repeatable.
December 2013 in New Zealand | |
Battery age | New |
Avg gen run duration | 2:09 |
Avg time on batteries | 6:53 |
Gen runs/day | 2.5 |
Max battery duration | 12:30 |
% time on gen | 22% |
% time on batteries | 78% |
The table above shows our normal operating mode in New Zealand in December of 2013 on freshly installed batteries. We treat the boat like a small apartment so our power consumption is high for the size of the boat. Our at-rest draw tends to run in the 35A to 45A range at 24V (840 to 1080W) and often runs higher. We could conserve more, and many do, but this is our home and we like to be comfortable.
When charging, we charge fairly hard where the early part of the charging cycle we will be charging at 250 to 275A at 24V. With new batteries, on average the generator can charge the batteries in just over 2 hours, giving us about 7 hours on batteries until the next generator charge cycle. With new batteries, the generator was running 2.5 times per day for 22% of the day, and the longest we went on batteries without charging was 12.5 hours.
January 2016 in St. Helena | |
Battery age | 2 years |
Avg gen run duration | 1:46 |
Avg time on batteries | 6:24 |
Gen runs/day | 2.7 |
Max battery duration | 9:22 |
% time on gen | 20% |
% time on batteries | 79% |
Avg daily kWh | 28 |
The next table (above) shows how the batteries were operating after two years of live-aboard use. We didn’t pull the exact number, but we know these batteries had 1,500-1,600 cycles at 4 years, so at this point we would expect they will be in the 650-750 cycle range, or roughly halfway through the lifecycle they will get on board our boat. Here the generator charge times are now 1.75 hours on average instead of just over 2 hours, and the time on batteries has decreased to 6.5 hours on average from nearly 7. This shows the battery capacity is slowly reducing as they age.
The margin of error on this data is fairly large since the loads will fluctuate, but the trend is clear. New batteries that were delivering nearly 7 hours between charges now are down to an average of 6.5 hours, and average charge times have decreased from just over 2 hours on new batteries to 1.75 hours at mid-life. These batteries still are in good shape, but are showing some loss of capacity.
September 2017 in Orkney Is, UK | |
Battery age | 4 years |
Avg gen run duration | 0:56 |
Avg time on batteries | 1:41 |
Gen runs/day | 9.0 |
Max battery duration | 4:13 |
% time on gen | 35% |
% time on batteries | 65% |
Avg daily kWh | 43 |
The table above shows a very different picture from 2 years ago, where charge cycles were 1.75 hours on the gen and 6.5 hours on battery. This is two years later as the battery bank nears end of life. The charge times are down to an hour and the average on-battery time is down to 1 hour and 40 minutes. The generator is now running 9 times a day, and the longest we went between charges is 4.25 hours.
These batteries have less than a third of their original capacity, but they are still functioning fine and the boat is still operating the same as ever. We’re no less comfortable in the Orkney Islands area with tired batteries than we were in New Zealand with new batteries. The only difference is the generator is running more frequently.
What we find interesting is the actual percentage of time the generator is running each day with end-of-life batteries is not that much higher than it is on fresh batteries. The generator just runs more frequently for shorter times. At end-of-life it is running on average 9 times a day rather than less than 3 times per day but the percentage of generator run time each day on new batteries in our usage cycle is about 20% on new batteries and 35% on end-of-life batteries. Running batteries down to very low storage capacity is possible without substantially changing the percentage of time the generator runs each day.
May 2018 in Norway | |
Battery age | New |
Avg gen run duration | 2:04 |
Avg time on batteries | 6:57 |
Gen runs/day | 2.4 |
Max battery duration | 8:19 |
% time on gen | 20% |
% time on batteries | 80% |
Avg daily kWh | 29 |
The table above shows Dirona back on new batteries and this data from Norway closely parallels what we saw with new batteries in New Zealand. We got on average 7 hours on battery and spent 2 hours running the generator to charge them.
April 2020 in Scotland | |
Battery age | 2 Years |
Avg gen run duration | 2:21 |
Avg time on batteries | 6:26 |
Gen runs/day | 3.2 |
Max battery duration | 7:30 |
% time on gen | 27% |
% time on batteries | 73% |
Avg daily kWh | 39 |
Above is the data on two-year-old batteries at the Isle of Gigha in Scotland. Again we see the data is similar to what we saw when our previous batteries were two years old in St. Helena. The average time on batteries in Scotland is 6.5 hours, with 2 hours and 20 minutes to charge. The maximum on-battery duration is quite a bit lower, 7:30 compared to 9:22 in St. Helena, likely due our heating the boat in the colder Scottish climate.
This most recent data shows another interesting phenomenon. We’d been sitting in the same anchorage for the entire month without moving the boat due to the UK being in lockdown attempting to control the spread of COVID-19. The boat hadn’t moved during this period and, of course, the boat hadn’t been plugged in. As usual, we spent about 70% of each day on batteries and, in our operating mode, we do 3-4 charge cycles a day and did 122 cycles since the last time the boat moved. In this short time, our battery capacity had reduced from the 6 to 7 hours of time between charges on battery and 2:20 min to charge down to 4.5 hours on battery and only 1.75 hours to charge. This is a serious degradation in 122 battery cycles and only 5 weeks.
This rapid degradation is caused by short cycling between 55% and 85% state of charge and not fully recharging during this extended period. It’s far better to fully charge lead acid batteries, but doing this frequently is inefficient. They can be charged to 85% in around 2 hours but fully charging the batteries takes closer to 5 hours. Certainly, this can be done but it’s a long time with the generator at very low load and it would mean the generator is running half the time. It’s not what we want, so we don’t do it and it’s an interesting experiment to learn about the long-term effects of prolonged short cycling (not fully charging).
A practical alternative is to fully charge once a week or every three days. This is much better for the batteries and is convenient for the operators, since laundry and other electrically intensive jobs might need to be done weekly. And this mode of operation is almost as good as always charging fully. We probably should move to this operating mode, but we’re engineers and like to see the results of running in different operating modes. So we only fully charge when underway on the main engine and, as a result, can end up with long periods of short cycling. Most of the capacity lost by short cycling will come back after equalization but not all of it. We’re interested in seeing how much equalization brings back. That data may cause us to move to a weekly full charge model and will give us a chance to see how much better that operating mode is on battery capacity degradation.
Summary
The table below combines the previous data, for ease of comparison, and includes some additional metrics on the calculations.
What we see from the data is mostly unsurprising. Battery lifetime usually slowly degrades over time. At least two distinct forms of degradation are in fact happening at the same time. One is the overall decline of the battery bank capacity over its lifetime—this takes years and hopefully more than a thousand cycles. The other form of capacity reduction is the short-term reduction caused by short-cycling. Both forms of lost capacity, but particularly the latter, can be partly restored by periodic battery equalization.
Our data shows a gradual decline from day one to end-of-life. And, overlaying this steady reduction is a saw-tooth, up-and-down function due to the negative impacts of battery aging and short cycling and then the partial capacity improvement contributed by battery equalization.
The part of our data that we find a bit surprising is the number of cycles that batteries can run if maintained reasonably well, aside from being short cycled. The negative impact of short-cycling is serious, but mostly is short-term and largely correctable by equalization. Another point in this data that surprised us is when operating with very poor-capacity battery banks, the percent of the day where the generator is running isn’t really that much longer than when using a new set of batteries. The generator is just on more frequently but for shorter periods.
The data also shows that battery lifetime can be remarkably long in terms of cycle count if the batteries are never excessively discharged and you are willing to operate on a substantially reduced capacity battery bank.
Overall, we’re pretty happy with our AGM batteries. We’ll eventually move to Li-Ion but the price/performance of lead acid remains pretty impressive so we’ve not been in a rush to make the change.
So I have some interesting data. When building my auto-start system, I first went off of your “55%-85%” band. Typically, this resulted in my generator running for about 90 minutes. However, after only 2 or 3 cycles the battery capacity was already going down noticeably, which seemed misaligned with what you were describing. The only way to get it back was a full charge (which was also taking more like 8 hours versus the 4-5 I would have expected).
However, one thing I noticed is that you are also charging for 2 hours vs 1.5 hours when the batteries are at full capacity. Clearly our charge and battery capacities are different, but I was curious if that extra half hour was making a difference. Sure enough, after going to 2 hours the capacity is more or less constant after a half dozen cycles (haven’t gone more than that).
I’m far from fully understanding it yet and have more experiments lined up, but it was definitely interesting how big a difference another 30 minutes charging made when doing partial charges.
Nice work Alec. It’s funny but I’ve ended up heading in the same direction. As a consequence of bringing the data together in this article, we were surprised by the loss of capacity being so large. In many ways, it’s an unusual test case where we just weren’t underway and weren’t moving the boat and only on generator for many weeks. In looking at this data, we made two changes. The first was to fully charge the batteries once a week. We long knew this was a good procedure but didn’t really have the data to prove it so didn’t do it. It makes a big difference so that is now policy and it’s easy to do on laundry day.
The second observation is the one you are making here and we agree with you. Rather than charge to a time, we charge to an battery acceptance current. Where we used to charge down to 35A acceptance rate, we started to experiment with lower values and have ended up using 23A as our charged level. That’s about 1:40 but our batteries are getting old. I suspect on new batteries it would be way more than 2 hours. At this level our 3 year old batteries with high cycle counts are doing very well.
I don’t know if we will leave the gen shut off threshold at 23A with new batteries but it’s working very well right now. We put the min charge acceptance rate in the user interface so it’s easy to change. We expected to change it a lot but ended up pretty quickly landing on 23A and we haven’t changed it for around 7 months and probably won’t until we get new batteries and perhaps not even then. Hopefully these batteries will continue to perform as they are for another 12 months.
Overall, we find having the data is super useful. But, you have to look at it :-). We probably should have really looked at the data years back but, in doing it last year, we made a couple changes one of which seems to closely match your findings. Thanks for letting us know what you have been learning. We’ll do a follow up note when we end up having to change the batteries.
Wow, 23A is lower than I’d expected for 85% SOC on a 1020 AH battery bank, but it clearly works well for you. That’s a very useful datapoint.
Again, you’re right. 23A is far higher than 85% charged and it’s what we have been using it for the last 6 months. I don’t know what we’ll use when we next get new batteries but this set is 3 years old and are now at fairly high cycle count. Prior to this year, we always used 35A acceptance rate but we have moved this threshold down to 23A as a consequence of looking at the data we blogged here, experimenting a bit more, and concluding that 23A gives far better battery life without unreasonably extending the required charge times.
On these old batteries, 23A is about 1:40 generator charge times when starting the charge when the trailing 15 min max voltage was 24.5V. That latter data point is estimated to be 55% charge using the Lifeline Technical manual 20 hour discharge rate voltage at 55% (60% is 24.6 and 50% is 24.3).
Have you thought about using charge curve slope/derivative as the threshold, instead of current? That feels like what we’re after here more than anything, and I wonder if that would be more flexible as batteries age versus just a fixed acceptance current.
Amazing, your thoughts exactly match ours on this issue. Really good question. Yes, we date take the 1, 2, 4, 8, 20, and 120 graphs and put them all into a high dimensional polynomial curve fit algorithm and knowing how accurate the 20hr curve is, we was very optimistic this would produce excellent results. It didn’t. We think the problem is the battery takes a long time to respond and stabilize after load changes and the high draw voltage to SOC graphs are full of error. The data tended to swing all over the place. We thought about it a bit and decided that we should focus on just do a polynomial curve fit on the 20 hour curve and it was far better. That gave us a F(V, A)=> SOC and it was much better but really not great. Acceptable but not great.
Our exploration of different ways to improve on SOC computation continued in our spare time for about 18 months. The best model w came up with is to use the Mastervolt computed SOC and focus on correcting the accumulated errors in this data. Normally the Mastervolt SOC only recalibrates for algorithm drift at 100% charge. What we did was calibrate it once daily when the boat hit a stable minimum charge rate in the middle of the night (but only if the boat actually hit min charge and wasn’t running). That worked pretty well. The second problem we needed to correct for is the Mastervolt (or anyone else) has a fixed battery capacity where, in actuality it’s decreasing slowly over time. We was able to correct for this fairly accurate as well and the net was this approach actually did produce a better SOC that any SOC gauge we had ever used in the past.
The problem with the best system of SoC calculation we ended up with, it was a bit ad hoc and we found we would make subtle tweaks every few weeks to months and the system was OK at estimating SoC and really good at starting and stopping the gen. But, it still wasn’t great and we could see material error on the SoC display every time we looked at it. We both hate complexity that doesn’t really deliver material value so we then decided to remove the SoC displays throughout the boat entirely and just ignore it. We then set up the generator autostart to start the gen when the min voltage over the last 15 min was less than 12.5V. And, we stopped it when the battery acceptance rate over the trailing 5 min was 35A (later changed to 23A).
Ironically this new system is less accurate than our previous attempts but it’s also simpler and, once set, we just left it there for 6 years until this year when we lowered the gen shut off acceptance amperage. Basically what we’ve done is find values that work for the batteries and, after that, we just ignore SoC entirely, don’t really notice when the generator starts and stops, and generally we’re happier and the system appears to be more stable and to adapt better to battery capacity changes both over time as the batteries age and between equalizations. In this case, simpler worked well. Find good values for the gen and don’t even bother to display SoC.
Very interesting. The noise you talk about on the battery voltage makes sense in terms of generator start. Though since in my experience battery voltage declines linearly as capacity goes down, it makes the polynomial approach less useful there. But since charge acceptance decays logarithmically instead of linearly, and in my experience it tends to be less noisy, I would have thought that would be useful to use some sort of polynomial, but it sounds like you were just chasing your tail on that one as well. Now I’m _really_ curious and need to collect more data! I haven’t gotten scientific enough about it yet (just using the N2kView graphs), so now I think it’s time to invest in the VDR100 and crunch some numbers for real.
In the mean time, completely agree with you on simplicity being important, especially on a boat that already has enough complex systems as it is. I actually can’t even do charge acceptance generator shutdown with my current signaling system (which is still driven by the inverter), so it’s battery voltage and time for me. I could drive it with N2KView but I’ve had a few occasions when that system gets confused and I haven’t developed your clever watchdog yet, so I’m not yet willing to rely on it for mission-critical workflows. Either way, this approach is definitely simple but as the batteries age it will need more manual care and feeding I’m sure. Once I have more data I will consider if it’s time to build an intelligence and resilient signaling system.
Stay tuned!
The curve fit works fine for stable loads. Basically SoC can be reliably delivered for a given battery technology as a function of voltage and amperage. The lifeline 20hr discharge graph in the technical manual is pretty good. If you are discharging at the amperage rate that would lead to a 20 hour discharge, then that function of voltage works well. I used a polynomial curve fit because it’s not a straight line. But, there are lots of times when this doesn’t work the most obvious of which is when charging. But the model also doesn’t work well when the discharge rate is uneven. If you sometimes have a hair dryer on (4 hour discharge rate) and sometimes have nothing on, the relationship between voltage and Soc breaks down. Essentially F(V)=>SoC only works when the battery draw is constant. That’s why I went with adding all the discharge rate curves and modeling it as a surface rather than a curve. Essentially F(V,A)=>SoC. But it turns out that changes in amperage draw take many seconds to minutes to stabilize. All solvable problems but I’ve really come to like just using the max voltage over last 15 min as a start signal and I’ve not changed that setting in 6 or 7 years. It’s simple, doesn’t trigger early, and doesn’t seem to need tweaking. The use of acceptance current for shutdown seems pretty simple and is fairly stable. I ran it without change for 6 years before adjusting down to 23A this year. I didn’t change anything during the lifetime of the previous set of batteries.
Battery voltage will cause you to frequently start the generator early when a load hits but that doesn’t do any harm. Charging for fixed time periods isn’t ideal and it will cause you to run longer than needed if you early started but, again, that won’t do any harm. What you have is very serviceable. But, if you want a fun project, you could get a Raspberry Pi and plug in the NMEA0183 bus into a serial connection so you can read battery voltage and charge rate. With that you can have all the control you like and it can turn the gen off and on by changing a GPIO pin driving a relay. $50 and not much work and you would be able to implement whatever you want and even record data over time. Or you could stick with what you have which is essentially what we used for a year and it was just fine.
Yeah makes sense, as it happens my ‘battery voltage start’ setup actually includes a time component as well. The Victron charger/inverter setup I have is “start the generator when the voltage is below X for Y minutes”, which is basically the same logic you use. Unfortunately ‘Y’ only goes up to 300 seconds, but I’ve actually still had good luck with it and mostly avoided the early starts you describe.
Makes sense. What you get out to 5 min, the chronic early start problem is minimized. 600 to 900 seconds would be better but it makes sense the system as it currently is now is working well.
A simple change you could try is to add a timer in the start signal line. With this you could put a 5 min delay on the on signal such that you only trigger “on” when it’s been
“on” and stayed “on” for 5 min. This would get you 10 min (or 15 if you preferred) trigger time time at low cost and and complexity.
Hi James,
First off, you’re so right that cruising with a generator auto-start is a complete game-changer. I just don’t think about battery SOC on a regular basis any more, which is really liberating.
Of course this now has me thinking about how often I should fully charge, which this article has a lot of great info on. But it has me wondering: How are you deciding when to stop charging? You mentioned that you go to 85% but how do you know you’re at 85% when you stop? Are you using charge acceptance current as a proxy, or do you have another trick?
Yes, essentially as you said. I use a SOC meter which is fairly accurate on the first charge/discharge cycle. The SOC meter gives us calibration on acceptance current. The SOC meter will quickly degrade in accuracy on charge/discharge cycles so we only use it to calibrate the charge acceptance current measurement and that’s what we use to shut off charging.
Great write-up James. I live in Western Australia where we have a lot of remotely powered things in the desert which means photo-voltaics are often combined with battery technology. The favored battery variant to allow a large number of deep discharges is the AGM-Gel VLSRA variety which are also called “OpzV’s”. I have installed 12 X 2v of the long tall tubular OPzV variety on my boat. I bought them from a German manufacturer (BAE) but they are also now made by well regarded marine electrics company Victron (see https://www.victronenergy.com/upload/documents/Datasheet-GEL-and-AGM-Batteries-EN.pdf ). There is a pretty good video on them here https://www.youtube.com/watch?v=kxiNpJlTbhI . I have been very impressed with the performance (80% discharge with NO loss of ongoing life) and durability of these units compared to my old lead acid batteries.
Thanks for the battery tech pointer.
This is really interesting and timely. I am in the process of installing a trolling motor on my 20′ center console. Mounting the motor has been the easy past. Learning about the power required is more involved. I chose a 24v motor since the space for additional batteries is limited. My first decision is what type of battery to install- Flooded, AGM, Lithium? Lithium is out due to their extreme cost. I seriously considered AGM to reduce the possibility of the battery’s electrolyte sloshing about in the enclosed center console. However, a “maintenance free” flooded battery is fairly well sealed but for a couple of small vents in the caps and the flooded batteries are the least expensive while providing the required amp hours. Group 31 will fit and provide 105 AH, enough for a day of trolling for fish. The other issue I have had to study was wire. I initially thought I could keep the wire run down to 10 feet which would allow the use of 8 awg stranded marine wire. However, once I located the conduits below the deck, the run turned out to be 28′! So, 6 awg will be used ( the motor will briefly pull 58 amps and is fused for 60 amps ). All through the installation the greatest challenge has been getting parts. The local West Marine has nearly bare shelves and there is no other option where I live. I have had to rely on Amazon a great deal. Even so, no one Amazon vendor has all the bits I need. Thus it has been a process of locating the part, ordering it and…waiting. At least I am locating the parts, and tools. The waiting takes some getting used to having been spoiled, pre-pandemic, by rapid delivery times. While waiting, I am educating myself on deep discharge batteries. Since two group 31 12v, 105 AH batteries are a significant cost I want to use them in a way that maximizes longevity. Two years ago I installed a second battery using The Blue Seas second battery kit. This includes a battery switch with, off, on, both (for emergency starting) positions as well as an automatic relay device that determines when and which battery needs charging off the engine’s 65 amp alternator as well as start isolation. With the downtime, waiting for deliveries, I am learning about those things you discuss here. My brief study on deep cycle batteries tells me that my battery can be run down to 80%, or about 9.6v. You mentioned running batteries to 50% of capacity without damage. Is that possible on a single 12v battery? I also note that my 2 year old battery will not charge past 11.5v. Based on what you write that seems to be a reasonable loss of capacity for a battery of this age. I also note that my 3 year old start battery will charge to 11.5v. I am thinking of installing a battery meter with a low voltage warning to avoid running the deep cycle house battery below 9.6 volts. I could just use it until all my electronics shut down at 9 volts, but I don’t think that would be good for those devices. Anyway, very interesting article. Thanks for taking the time to write it.
The advantage of Li-Ion is the battery capacity will take less space and size. Mostly because Li-Ion has high energy density but also because you can run a Li-Ion bank down nearly all the way. When using flooded lead acid, valve regulated lead acid, or AGM they will last much better if you don’t draw them all the way down. Taking them down to 9 volts is very hard on them and you will not get high cycle counts that way.
Worth thinking through putting two batteries in in parallel and only drawing the bank down to 50%. You deffinitely should have a voltage meter on the boat and you should have a state of charge indicator as well.
I didn’t understand your points of charging to 11.5V. When charging, you should be using bulk and absorption voltages of around 14.5. If you don’t get to 14.5, you may have a charging problem If after charging at 14.5 until the amperage flow into the battery is down to whatever the manufacturer defines to be full charge but on a single battery it’ll be down below 2 to 3 amps when it’s fully charged. If what you mean by charge to 11.5V, that when you charge it fully at 14.5 and then disconnect the chargers (without any other load), it drops down to 11.5V, then that battery is pretty close to having no capacity at all. Not sure what you mean but if you see 11.5 without any load on the battery, it’s either discharged or, if it was just charged, the battery has very little capacity remaining.
Basically, consider using enough battery capacity to be able to not run below 50%. I suspect you’ll find a group 31 won’t come close to giving you a full day of trolling unless its a very small boat and more efficient than I’m guessing. Charge at 14.5 bulk and absorption. Install a voltmeter for sure and consider installing a state of charge meter. Good luck on your project.
Very nice write-up of your battery data.
Have you ever thought about a de-sulferating charger / tender to help with the short cycles? (Granted I don’t think anyone would have planned this event we’re in)
https://www.batteryminders.com/
I think you mean watts instead of kw:
Our at-rest draw tends to run in the 35A to 45A range at 24V (840 to 1080kW)
Lifeline, the battery manufacturer, recommends conditioning (more generically called Equalization) which is a carefully controlled prolonged charging at temperature corrected elevated voltage levels so we use that procedure rather than desulphating chargers.
You are right, I mislabeled that kW rather than W. Thanks, I’ll make that change.
Brian
If you have a Victron Multi, you can remotely equalize, with their app’s and VRM website.
That has been a saving for us watching and maintaining our boat 4,000 miles away
Impressive. That’s a pretty cool feature.