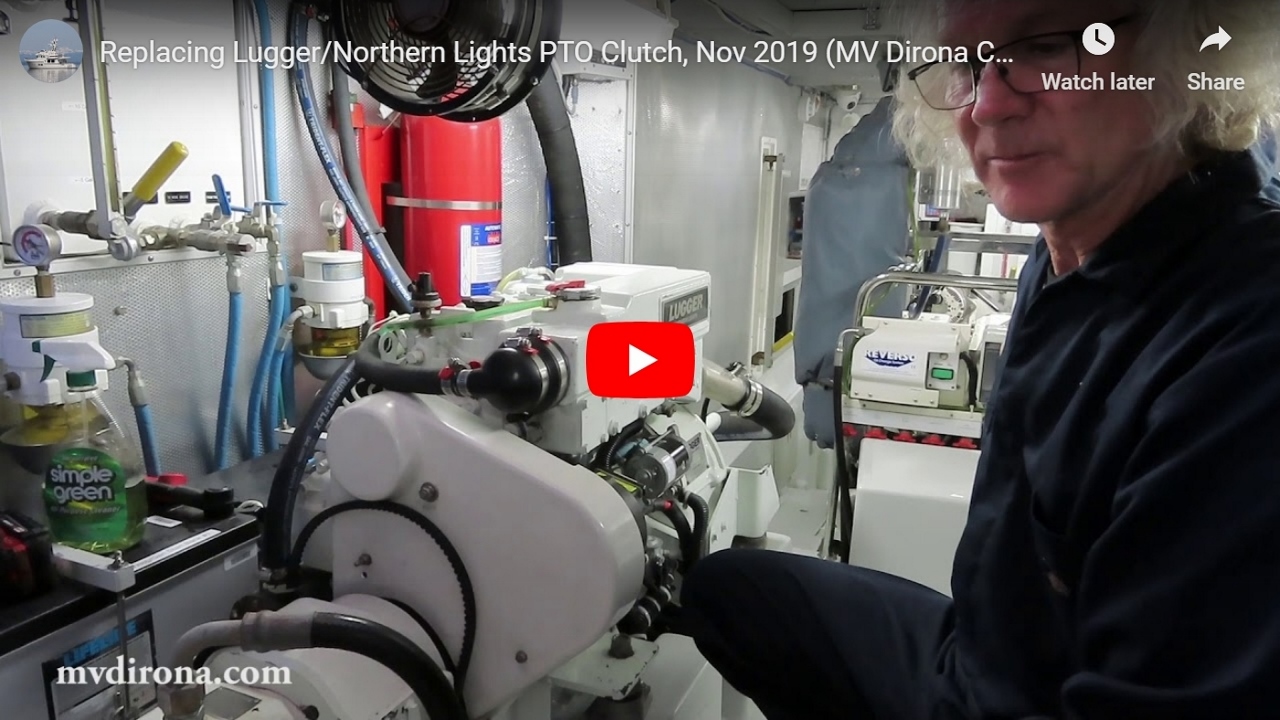
Many small Lugger marine engines and Northern Lights generators are equipped with a power takeoff (PTO) unit that can be used to drive accessories. Hydraulic pumps are a common use case for this PTO.
These PTOs are equipped with electric clutches to allow them to be powered or unpowered at will. This is convenient, but the clutches are a wear item that periodically require service. In this video we replace the clutch on a Lugger L844d auxiliary engine with 1036 hours on it. This same clutch and PTO also is used on the Northern Lights 12KW and 16KW generators.
BTW can you point me at sources for the pump and clutch please? And some idea of cost, in case these places all say “call for quote”. I just want to put some numbers into a budget for building out this system. Thank you!
Chris
The system are sold as complete systems. Focusing first on the Wing or Gen, as an option Northern Lights has a clutch driven PTO that can be ordered on their generators are propulsion engines. I think the clutch is available from Pitts Industries for a bit less than $1000 but it wouldn’t do much good to buy the clutch directly since you still need all the custom mounting hardware for it. That part of the system is usually purchased as a system from the supplier for wing engines and generators.
On the main engine, medium sized and bigger main engines usually have PTOs ready to go. On our Deere 6068AFM75, there is a PTO available but there isn’t enough clearance there for a large hydraulic pump. Our transmission is a ZF 305-2 and it also has a PTO and it has sufficient clearance and that’s what drives our Rexroth 45CC pump.
The hydraulic system as a whole is sold as a package from American Bow Thruster (ABT) as part of there design for stabilizers and other hydraulic components. The parts can all be purchased independently but it was a package purchased on Dirona so I don’t know the prices for each component. Many components like the stabilizers themselves and all the control systems are custom made by ABT and only available from them as part of an overall system. These are often installed on new boats but ABT is happy to help with existing builds. ABT does nice designs with a focus on reliability and their customer service is simply unbeatable. They are head and shoulders above most of the marine supply industry in their approach to making reliable gear that really works and standing behind it.
Thanks again James. Very helpful knowing I can approach ABT for a solution. My general plan is based on the notion of adding the second hydraulic pump to the wing engine of a Nordhavn that is already equipped with the pump on the main, to add redundancy for the stabilizers and capacity to run hydraulic thrusters and a bilge pump. Ideally the finished system will look just like Dirona’s, I would certainly rather rely on an established engineering firm rather than becoming a parts supplier, fabricator, and hydraulic engineer myself! :)
Chris
Almost all larger Nordhavn’s are equipped with hydraulics and it’s common to have two pumps where one is on the main and the other is on the gen. for systems equipped with ABT Stabilization at Rest (STAR), they also have a large electric motor driving a hydraulic pump. This electric motor can be driving by any of the generators on board. So, on the larger boats, there are lots of options.
Most Norhavn’s in the 40′ to 52′ only have hydraulic stabilizers but use electrics for other accessories. For example, our boat is #63 in the 47/52 series and, in all those boats, 63 is the first all hydraulic boat. Many of the smaller boats use passive stabilization and some don’t have any hydraulics at all. So, when looking at Nordhavn’s you’ll see the everything from hydraulic everything to no hydraulics all. Generally, adding hydraulic stabilizers is a pretty large and expensive change but, if the boat is already hydraulically equipped, adding more hydraulic equipment is quite practical.
That’s the way I see it. Mine will be the first all-hydraulic 47 (albeit non-factory). Clearly no 47’s were full hydraulic from the factory and I know that the first ten or fifteen hulls didn’t even get a 24V electric system. There’s zero probability that I will have a 47 with 12V electric or no stabilizers, but a good chance that the one I buy will have no stern thruster. I will definitely want a stern thruster, and I will definitely want the redundant hydraulic power for stabilizers if nothing else. So if I’m going to the trouble of installing a stern thruster anyways I might as well make it a hydraulic one, gaining 100% duty cycle operation, possibly proportional thrust control, and upgrade the hydraulic system to support it. Then I can redo the bow thruster with a hydraulic at the same time or later as it suits me. A few $$$$s? No doubt. Personal satisfaction and ease of operation? Maxed out. :) Yeah, I’ll probably be puttin’ that jackscrew socket holder into the steering ram mounting plate too :)
It’s sounds like you have thought this through carefully and know the market fairly well. I think you are right that a 24V boat is better than 12V in that it allows smaller conductors but, from my perspective, a 12V boat might not be a show stopper. On the hydraulics front N4715, Oso Blanco, was the first N47 delivered with a hydraulic bow thruster. Between N4715 and our N5263 which is an all hydraulic boat, I don’t know of any others with even an hydraulic bow thrusther. There may be some I don’t know of but I think you’ll find it a fairly rare configuration in the 47/52 series. If you include the N55 in your search, you’ll find more hydraulic boats in the market.
I agree with your preference for hydraulic bow and stern thrusters. On the 47/52 series, the additional advantage of hydraulics is they come with greater power. The 47/52 series when we purchased Dirona used 10 hp electric thrusters whereas the hydraulic option was 18 hp proportional thrusters.
Oh, yes, for sure the greater power in the thrusters. I look at these older boats built with 10HP or less electric thrusters… no way. And I think that may be some of the drive to the 24V electric system, to support higher power electric thrusters. Then you’ve got the windlass and davit crane which would typically be electric, even if the crane itself is hydraulic (or at least I’ve seen configurations where this is the case). I can definitely see the argument that 12V electric is sufficient when you go all in on hydraulics. Interesting thing to think about.
I really love the 55/60 for its floor plan and I agree there will be more hydraulic configurations available in the brokerage market. A decent 55 will go over $1M and I’ve seen a survey report on one hull that would have added $200K in repairs to a sub-$1M sale. Not that I don’t expect problems in an aging boat, but I have to draw a line on my budget somewhere. But they are a fabulous design.
I like the 55/60 layout as well but, as you said, they are typically somewhat more expensive than the 47/52 series and we’ve been pretty happy with the 52. We do really like the hydraulic equipment on Dirona. We have Windlass, bow thruster, stern thruster, emergency bilge pump, and stabilizers. The crane is hydraulic but it runs on a separate hydraulic electric power pack so is effectively an electric crane.
With the hydraulic system, you have redundancy with the PTO on both main and wing, but if the main engine should fail, the wing has to be properly sized to be able to run hydraulics and drive the boat and a reasonable diminished speed. I am sure you factored this in when doing the specs on the boat, what flexibility did you have when choosing a larger wing or was the original spec wing sufficient to run hydraulics and prop?
Yes, good point. It’s important that the wing have the power to drive the stabilizers and the propel the boat. When running the thrusters or anchor windlass, it really got any power left to do anything. But, the stabilizers require very little power so it has no trouble running both the stabilizers and propelling the boat at the same time. In the few times we have run it in open ocean (twice doing a repair and once doing a main engine oil change), the wing did a great job. The repairs were 3 to 4 hour operations so the wing got a good test both times with the stabilizers and it did great.
In my opinion, the wing on our boat would be better sized at 50HP or, potentially, even 55 to 60HP. The 40 has no trouble delivering just over 4 kts but it’s running at pretty much max output when stabilizers or windlass is used. I would prefer more HP but, with tuning, a 40hp can deliver full hydraulic operation — it just works hard to do do it.
One more question, sorry. At times when an anchorage has waves rolling in, like swell from around a headland, then to use the stabilizers, some power source needs to be on to run the hydraulics, running the wing with a light load would not be a good idea, a slightly over sized 16kw generator with a PTO might be an alternative?
When Dirona was built, the hydraulics and stabilizer supplier (ABT) didn’t yet offer STabilization At Rest (STAR). For those boats that are so equipped, they use an electric pump that can be driven by any of on board generators. For us, if we are in a rough anchorage, we deploy a passive stabilizer. But the boat is heavy and doesn’t roll much so we seldom deploy the flopper stopper. However, the few times we have needed the flopper stopper, we really needed it.
Because STAR comes with larger fins and this is useful even when underway in particularly rough water, we probably would chose to install it but we might choose to go with the flopper stopper as well.
Hello James,
The video on clutch replacement was excellent thank you!
We have a Northern Lights M843NW3.3G 12KW Generator with Rexroth A10V045DFR/31L PTO. Our Trawler has a full ABT TRAC hydraulic package, to include GETHOME and STAR. The Armature and rotor in the clutch are ringing against one and another when the clutch is disengaged. When clutch is engaged, the front bearing cannot handle thrust load and is getting damaged.
Is PITT Industries the sole supplier of clutches for Northern Lights? Is your clutch a 24Vdc PITTS part number 13814 that you installed on your Get Home? Do you know if that crosses to Northern Lights Generator 34-30032? We have a 12Vdc version Northern Lights Clutch 34-60031.
The sound you report sounds exactly like mine sounded when it first failed after only a few months of use. The system was torn down on warranty and there was no sign of interference but the bearing had failed. The noise that sounds like interference between armature and rotor is brinelling of the bearing. The bearing wear surface breaks up and, when it’s rotating, it produces a ringing noise. The ringing noise is the clutch outer components ringing due to vibration from the excessively rough rotating bearing.
The bearing brinelling was actually false brinelling caused by excess vibration when the bearing isn’t turning (clutch closed). While the clutch is closed which is normal for longer periods, the components will be vibrating due to normal 4 cylinder diesel harmonics. Eventually the bearing lubricating grease wears through allowing metal-to-metal contact and damages the bearing race. On rotation, the problem gets worse. Subsequent clutch engagements happen at a different location and that location will eventually be damaged as well. This can lead to very rapid failure (25 hours).
The solution is put a time on the clutch that opens the clutch every 50 min for 300 msec. This allowed the clutch to last 5x longer. I later changed to a 300 msec every 60 second timing and expect this might be better. In addition, we don’t leave the system at idle. We start the engine, and bring it up to 1500 or above and just never leave it at idle for more than a few seconds at a time. Finally, only leave the clutch closed when needed.
The above approach was quite effective in achieving good clutch lifetime.
James,
Thanks again for your January 30th response. You mention that the first clutch was replaced under warranty. How much time passed before the first clutch bearing failure? You also mentioned 45CC. CC is not specified on the Rexroth A10V045DFR/31L PTO supporting our Northern Lights Generator. The PTO label has a DR – Pressure controller rating of 280 bar and a Displacement per revolution (cm3) of Vg = 45. Does VG = CC?
Yes, you have the same Rexroth hydraulic pump installed on Dirona. Actually we have two of them, one on the main engine and one on the wing engine.
I forget the exact hours where the PTO clutch was originally replaced but it was fairly low. I think around 250 hours.
Thanks James. We have two Rexroth Hydraulic pumps as well. One on Main Engine and the other on the NL Generator. Both with a VG rating of 45.
I spoke to Hugh Brooks at PITTS Industries. As I’m sure you are aware, PITTS manufactured your replacement clutch. He is part of their Engineering Team. Hugh puts a great deal of emphases on proper shimming of the clutch to reduce unnecessary loading on the clutch thrust bearing that you illustrated in your presentation. I’ve been told that Northern Lights has an alignment tool that can be used as well. Are you familiar with shimming and the NL tool?
I have an identical failure. It sounds like there could be a risk in delaying the warranty replacement however you mention that you had observed the failure early on. On first discovery of the false brinelling caused by excess vibration when the bearing isn’t turning (clutch closed), how much time passed before you replaced the clutch? What does a “catastrophic” failure look like? Will it disable your GETHOME Engine or in my case the NL Generator?
The clutch will run for quite sometime with the bearing making a ringing noise. In thinking through likely failure modes, most aren’t catastrophic. The bearing could seize which would effectively close the clutch. The bearing could develop excessive runout which would lead to interference in the clutch which would destroy the clutch but probably not do other damage. There is a small chance in any rotating mechanical system that the system could “self disassemble” but this seems fairly unlikely to me. Some of the fault modes could damage the pump but, again, that doesn’t seem that likely to me.
The most likely failure modes is locking up and driving the pump which will take power from the generator but the pump you have is a variable displacement so it’ll destroke and the “tax” of driving the pump will be sufficiently low that you still have 70 to 80% of the normal generator output. I personally can’t live with taking the chance of catastrophic failure so I replace the bearings when they start making noise but I admit that the probability of this outcome isn’t high.
One R&D experiment that was tried on my second clutch was to machine it for a much larger and more durable bearing. This may have had some minor contribution to increases life but Pitts Industries argued that this would not substantially improve the false brinelling problem so we abandoned this line of work and focused on the three changes below.
Three operational changes were put in place to reduce false brinelling: 1) put in a timer that releases the clutch for 300 msec every 180 seconds and then reconnects it again (Pitts recommends every 1,000 seconds but I prefer moving the clutch more frequently), 2) only having the clutch engaged when needed to keep the bearing turning (it’s non-turning time that causes the fault), and 3) I idle the engine at 1,600 RPM and put it to 2,600 when in use (no low RPM idling). The last action is one already in place on your generator. Using this protocol, we found it’ll last many years but, in a generator application, you’ll have upwards of 10x the hours of our wing engine so might see faults more frequently.
Generally, prior to false brinelling occurring, minimizing the clutch engaged time is the best defense. Once false brinelling has occurred, the damage will continue to get worse whether engaged or not since the rough spots do damage while the bearing turns.
Yes, I do know of the Northern Lights alignment tool and it was tested during warranty and found to be in spec. Once aligned, if you do not put it out of alignment and ensure that the alignment pins are replaced on each clutch change, it should not go out of alignment. If the pump is out of alignment, it’ll damage the bearings but this form of damage is different from false brinelling. False brinelling is caused by the bearing not turning and just rattling around where as alignment problems will put excess load on the bearings.
James,
Your video and the Q & A have been tremendously helpful. Fair Winds and Following Sea to you and Jennifer.
Thanks Jeff and best of luck on getting your PTO clutch solid — we’ve had pretty good luck with ours.
James, Thanks for this great tutorial. I’m certain I will be using this information in my future boating adventures! Not only does this show us how to deal with the clutch replacement but it got me thinking again about having that redundant and also additive hydraulic pump capacity strapped onto the wing engine. I wish I were more knowledgeable about hydraulic systems. I’m an electrical engineer so I tend to think in terms of series and parallel circuits. My question is: are the two pumps pumping in series or parallel, and is it correct that there is no need for a bypass valve of some sort when only one pump is operating?
Thanks!
Chris
The two pumps have suction hoses drawing from the reservoir, pressure hoses that feed the same manifold, and pressure sense hoses from the same manifold. Where the pressure sensors enter the common pressure manifold there are large check valves (1-way valves) so that either pump can be used and pressure doesn’t leak back through an unused pump. It’s a nice design that offers a lot of flexibility.
Since you are familiar with electrical parts, hydraulics are really remarkably similar to think through. In this case the two variables are pressure and flow. In our system, the high pressure nominal output is 3,800 PSI and, at that pressure the thrusters will produce 18 HP. Say you are running only on the main engine and it’s idly and you use the thrusters there won’t be much flow so, as the thrusters are applied, the pressure falls fast and the output will be feable. At higher revs or on the wing engine at higher revs, there will be sufficient flow so the pressure will stay at 3,800 and full power will be available at the thrusters.
Hydraulics are actually very similar to electrical circuits where, if you have a source that produces 50A and 240V, the voltage will stay near constant as you increase draw but, if the load draws more than 50A, the voltage will fall. The interplay between amperage and voltage in an electrical circuit is very similar to the interplay between pressure and flow in a hydraulic circuit.
Thanks so much for this James. Indeed I have often used water flow as an analogy for electricity when explaining some electrical concept to a non-tech person. Mixing water and electricity. That always works well :)
I’m guessing that the pressure sensors are telling the pumps not to overpressure the system? Or is there some kind of feedback loop going on here where the pump is actually regulating pressure?
Thanks
Chris
The pumps are rotary designs where the pistons are pushed up and down by a swash plate. The angle of the swash plate is the piston stroke so the pump can be stroked up to a maximum, in this case 45CC per revolution, or down to 0. There is a pressure sense hose that runs back to the pump that controls the swash plate angle. When the system is “off” the pump is run with just enough stroke to produce 400 PSI which is enough to control the swash plate but not much more. If the stabilizers are turned on, the system moves up to 1,500 PSI. American Bow Thruster (ABT) uses 1,500 for the stabilizers since they don’t need much power to operate. If the thrusters are used, for example, the system strokes up to full pressure which, in our case, is a fairly high 3,800 PSI.
That’s incredible. See comment above about not becoming a hydraulic system engineer :)
Hydraulics are pretty cool. They can deliver massive forces in a very controllable way. And, the world has good experience with how to produce continuous duty hydraulic equipment so the thrusters, windlass, and stabilizer can run all day long. No thermal cutouts, no restrictions on use, they just work.
Hi James
Are you able to run both thrusters at (or near) full power on the wing engine alone? I know you have identical pumps on the wing and the main, and the main would be contributing some small amount of power even at near idle maneuvering speed, but a hydraulics installer company I have been talking with is telling me I could not possibly run those thrusters on the wing engine alone. Maybe you are counting on some power from the main, but it seems like this other guy is convinced that the wing and its pump would never be able to produce enough power for more than one thruster. I suspect he’s not comprehending that the wing is a 40HP engine.
Hey Chris, your hydraulics specialist is correct. By far the best solution is to have a 60 hp wing engine but I couldn’t convince Nordhavn to make that change. They are much more comfortable with the 40hp wing engine as designed for the N47/52 series. I think 60 would be a better sized engine whether using hydraulics or not but it’s open to debate and I have to admit the 40 can deliver 4.5 kts. I would prefer to see it working less hard but it does work fine for the application. When driving hydraulics, it almost has the capacity to drive the hydraulics but not quite. The solution to “not quite” has passed through a few iterations. I’ll explain what was originally done and the changes we made to get to full hydraulics output.
When the boat was in the design phase, the hydraulics manufacture explained to me that the Nordhavn 52 as normally built comes with 10 hp thrusters. I was installing a hydraulics system that was capable of delivering 18 HP running at the operational limit of 3,800 PSI. However, this would over load the wing engine so the proposal was to both rely on some output from the main engine and lower the hydraulic output down to 13 to 14 hp. The main engine power take off on the transmission is rated to a max torque of 20 ft lbs which limits what we can take from the main at idle. But if we take that 20 ft lbs and lower the thruster output to around 13 or 14 hp by dropping the hydraulic pressure to between 3200 and 3400 PSI.
This works but has a couple of downsides. The first is that it’s a fragile point where if the wing is not running at full rated RPM, it’ll stall. It’s right on the verge of stalling which isn’t great. And, of course, thruster output is limited but, overall, this package as delivered was more effective than the electric thrusters and it worked well. I didn’t like how near it was to stalling and running the wing at 2800 RPM is higher than I liked but it did work.
For a variety of reasons I don’t like engines idling at 600 RPM. It’s slightly more fuel efficient at low speed but most diesels are just more happy at higher RPM so I normally set them to 750 RPM and I much prefer them there. On an electronically controlled engine, it’s a bit more of a hassle to change RPM but, since I prefer 750 PSI I asked for it and the Deere distributor set it up that way for me.
It ran like this for nearly 2 years until one day I was landing the boat in a steady 25 kt cross wind and the thrusters where really struggling. I started to think about how nice it would be to have more thruster authority and, as I thought through it, I realized that I could draw more power from the main at 750 RPM than was possible at 600 RPM. I decided to dig deeper.
I worked the numbers and set the system up to not overdraw the main at idle but still deliver the entire 18hp available at 3,800 PSI hydraulic pressure. It worked and could deliver both thrusters at full RPM but it was a bit fragile in that the wing was still on the verge of stalling. The problem of having to run the wing at full rated RPM (2600 RPM) to avoid stalling was unchanged by we now had full thruster output. Having been rewarded by this progress, I got interested in what was possible.
The thrusters at 18HP were amazing so I started to wonder if it would be possible to achieve this configuration without the wing so close to stalling. Where I ended up is determining that the power available from the main engine at 800 RPM (+50 RPM from my normal idle setting), it delivered just enough more power while staying below the PTO torque limit that the wing could no longer be stalled. As before I have the full 3,800 PSI on both thrusters if the wing is running at 2800 RPM but if I slowed down to 2,600 RPM on the wing, it was still full output. And, even better, if I slowed down to 2,400 RPM, the thruster output would full slightly but the wing wouldn’t stall. In fact, if I drop the RPM down by 100 RPM increments down to around 1,500 RPM the thrusters get progressively more weak but the wing engine won’t stall under any circumstances.
In this configuration, the thruster output is 100% with the wing at 2,600 RPM (its full rated output is 2,800 RPM), at lower wing RPMs, thruster output goes down but the wing is nowhere close to overload. I didn’t mind the original configuration that much but having the full 18HP output is considerably better and, probably even more important, the wing is never over loaded or near stalling. The solution was, as you predicted, to draw more from the main engine. And, doing that required a higher idle speed to stay below the PTO torque limit but I’m fine with that and this is the configuration that I’ve been running for the last 8 years.
Thanks James, this helps a lot, and changes the cost equation for the project too because the existing pump on the main engine will have to be replaced with one that matches the high pressure/volume pump needed on the wing. Like you, I want all the power the thrusters are capable of for exactly those scenarios you described. I also agree with your thoughts on main engine idle speeds. Electrics for the thrusters are getting more cost competitive even though the basic component cost of a 15 – 18 HP electric thruster with proportional motor drive is nearly double that of the equivalent hydraulic thruster (and the motors are huge, of course).
More and more cost in upgrading the hydraulic power generation gear.
Side Power makes a nice 1000A DC motor drive for proportional control, which I can also use with the existing 10 HP bow thruster giving me more freedom of choice as to when to upgrade the bow thruster motor itself to higher power.
I’m a little worried about whether that monster electric motor will actually fit in the laz back there with all the steering gear in the way…
I would still put a smaller pump on the wing to give me stabilizer power backup.
Thanks again for all this incredibly valuable info. When you’re back on the US east coast again some day I hope I can repay the kindness!
Chris
Certainly electrics CAN deliver. There is nothing inherently wrong with electric thrusters. The reason they have a poor reputation is most recreational electric thruster systems use very light duty motors with poor duty cycles. Most are cost optimized and really not very good but certainly, with appropriate design goals, could be quite good. As an example of what can be done with well designed thrusters, during sea trials both of Dirona’s thrusters were left on full for 20 min. The boat just spun like a top in the middle of Elliott Bay Seattle. They never time out and just keep going.
I don’t recall what boat you were working with but, if it’s a Nordhavn 47/52, the rudder and steering gear aren’t close to the thruster so interference there won’t be an issue.
Generally, we vastly prefer the hydraulic systems on Dirona to the electric systems that were available at the time. Today, better electric options are available so that’s more of an option these days. I still think we probably would go hydraulic if we were making the choice again today but the decisions are complex and, I agree you need to carefully think through cost and ensure that any design under consideration is complete and fully thought through.
Agreed on all points. Yes, it’s a 47 I’m doing. For sure if it was a new build I’d go 100% hydraulics. I think what I can obtain for electrics today will do the job well, using basically over-provisioned motors and proportional control we can keep the thermal under control. Side Power claims they can run 100% duty cycle at 50% power and the installer I’m talking with says they’ve installed one with forced air cooling that ran 100% power for 20 minutes and was still running when they got bored and stopped it. I think battery capacity is the real bottleneck at that point. True, the motors are vastly more expensive than the equivalent power in hydraulics, but I suspect that difference will be quickly swamped with all the jewelry we have to add or replace to retro this into the existing boat.
Great to hear there’s room behind the steering gear for the thruster motor.
The combination of using a large electric motor and ensuring it’s well maintained, kept clean, and has big cables to a nearby battery (low voltage drop) will probably get you an excellent solution.